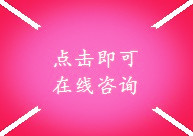
關于我們
高效超聲波焊接設備研發生產一站式供應商 始于2004
深圳市必能順超聲波設備有限公司成立于2004年12月,專注于超聲波行業23年,是一家專業生產超聲波塑料焊接機,超聲波熔接機,熱板焊接機的高新科技企業。公司自創立以來,本著"誠信待人,高效務實,質量為本,持續發展"的理念,堅持以專業的精神,過硬的技術,細致的服務,贏得了廣大客戶的一致信賴。
- 23年專注超聲波、熱熔焊接研發生產
- 先進的數字化智能超聲波塑料焊接技術
- 設備操作簡便,焊接速度快、焊接強度大、生產效率高
- 品種齊全/經驗豐富/多重檢測/售后完善
- 廠家直銷,品質穩定,一站式服務
專業提供超聲波焊接技術解決方案
多年專注超聲波、熱熔焊接研發生產,主營:超聲波塑焊機、熱熔機、超聲波清洗機等,品種齊全,經驗豐富,多重檢測,售后完善超聲波焊接設備供應商,23年專業經驗,一站式提供超聲波焊接設備使用方案
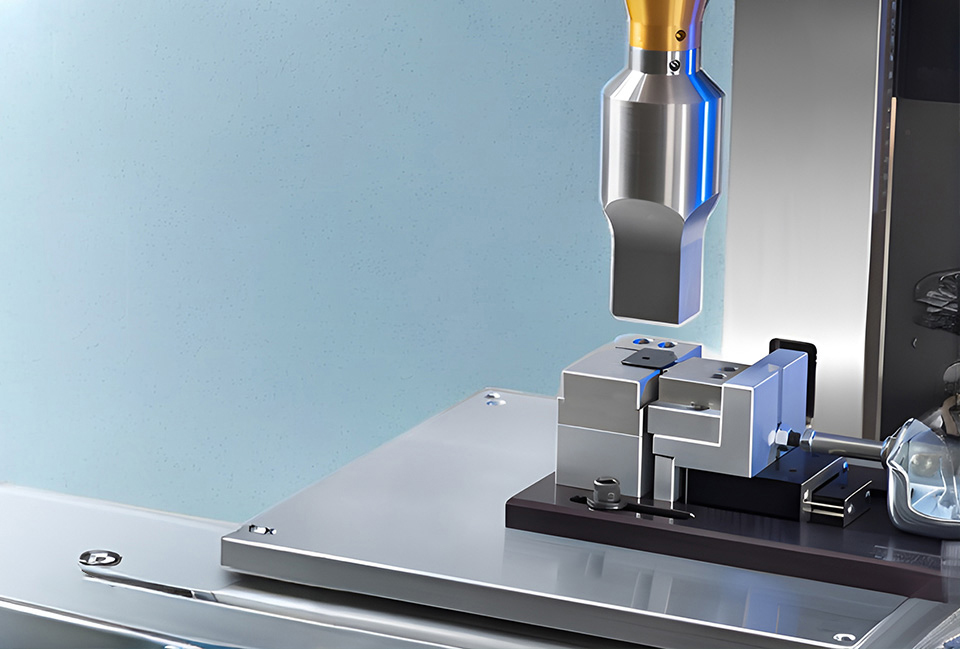
多年專注超聲波、熱熔焊接研發生產
產品中心
行業應用
專業超聲技術新聞資訊
新聞動態
聯系我們獲取更多消息
聯系我們